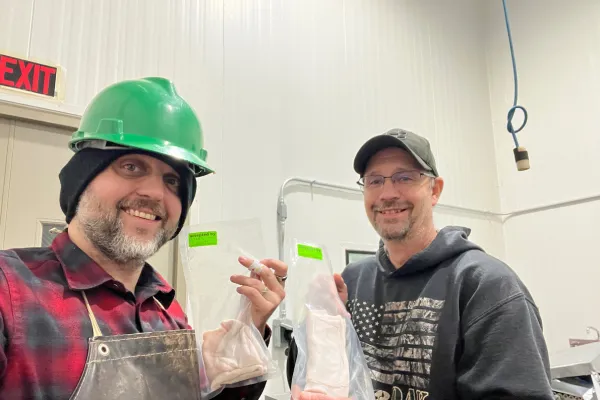
On breakthrough
Craig and I had been working on setting up a new machine. We removed various protective covers, and installed several belts, finally getting the last one correctly routed. I started wiring the plug but a screw was stripped and wouldn’t work on a brand new plug housing, so we ended up having to swap it out with an older and sturdier part we just happened to have on hand.
Craig is the plant manager at a processing facility I have been doing work at over the course of the past nine months. We’re looking to make corium, a collagen-rich material produced from cattle hides by removing the hair, flesh and other impurities. Craig and I have gotten to know each other fairly well over these months, and now was the moment of truth for our efforts. Will all of that work provide a good result or do I have to go back to the drawing board and try something else? As I threw the switch it turned green and the screen on the machine lit up. One hurdle passed!
After adjusting settings and changing the language preference, Craig and I looked at each other and I pressed the start button. It was almost a surprise that the rollers all moved in the right direction. A sigh of relief that we had gotten the wiring correct. Success! We were almost there!
Before Craig left for the day, I took a piece of hide that was already cleaned and prepared, cut it down to a shorter length and placed it on the feed tray. When I tried to feed the hide into the machine, it wouldn’t move forward… even at the maximum setting, it was just too thick. We moved the manual dial and got a little more play than the maximum setting, but still not enough. I turned off the machine and thought for a few minutes. Maybe this new machine wasn’t going to work after all…
Resolving to at least make a few more attempts at solving this problem, we decided the best path forward would be to remove the upper portion of the machine that was blocking the slightly-too-thick piece of hide from feeding into the machine and see if that would work. So I removed six bolts holding an upper roller in place.
With the inner workings of the device more exposed, we turned the machine back on and tried to feed the hide in now, but to no avail. Without the upper roller, it just wouldn’t feed correctly.
So we stopped the machine, and much like I had with a manual version of this machine, placed the hide partway through and then worked to re-secure the roller we had removed on top of the piece of hide, squeezing it into place. This did work, and we managed to process our first small sheet of corium, however unconventionally. This sheet of corium would be sent one week later as our first sample to a potential customer.
While thinking about how we were going to do this involved process for the remainder of the hide, I changed the thickness on the screen to do a second pass and discovered that the manual and digital settings were independent of each other. So if the manual dial was turned all the way in one direction, the screen setting was then adjusted to the maximum, and after this the manual dial was turned all the way in the opposite direction, we could get several extra millimeters of thickness! This seemingly small difference was enough so we could process the material without having to disassemble and reassemble the machine for each cut. We couldn‘t set the machine to this thicker setting on the screen itself, but the screen did show us the actual thickness when fine tuning the manual adjustment knob. We had managed to hack the machine settings so the opening was now thick enough such that we could feed the hide pieces into the machine directly.
A few more passes and we had the start of our very first commercial batch! Craig and I examined these freshly made sheets of corium, both impressed by the outcome, and we celebrated our success. It would be several more hours before I finally finished the effort, with my back and arms sore from the labor of processing 8 kg of material. Exuberant, I called my wife to share the good news that we had managed to deliver, and were now in business, the first commercial batch of corium was complete!
Facebook
Instagram
X
Youtube